MTM's circular chamber cleaning systems were developed for a multi-stage spraying and drying process.
They are suitable for large parts with simple geometry as well as for smaller workpieces such as camshafts, gear wheels and axle drive wheels.
The items to be washed are conveyed on a circular path through a closed tunnel in which the sectional treatment stations of the parts cleaning system are located. The simultaneous activity of several process steps with short cycle times enables a batch throughput of up to 1800 parts per hour.
Compared to conventional continuous spraying systems, MTM's circular chamber cleaning systems require significantly less space and can be easily integrated into production even where space is limited. The loading and unloading stations of the circular chamber cleaning systems are combined in one station. One operator is all that is required for loading. Robot loading and unloading at one position is therefore also easy to realize.
Systems type SKR (spray circular chamber cleaning system)
Requirement for MTM:
A space-saving system for industrial parts cleaning is required, which is designed for a multi-stage spraying process with subsequent drying.
The SKR-type facility offers:
-The process steps of loading/unloading, spray cleaning, spray rinsing and compressed air blowing as well as hot air drying take place simultaneously.
-The nozzle holders are movable and spray over the wash ware several times. This mobility of the nozzle holders significantly improves the spray pattern of the system compared to the fixed system used in continuous flow systems.
- Aqueous cleaners (pH value between 6-12) and cold cleaners are suitable as cleaning media. However, due to the spray cleaning process, the industrial cleaning system may only be operated with non-foaming cleaners.
-The parallel active times and shortest non-productive times enable a high batch throughput.
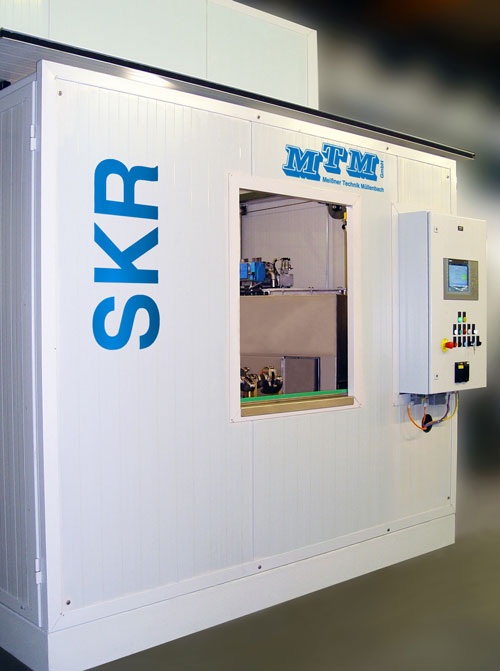
-This system is flexible with regard to the useful dimensions of the workpiece, the maximum weight and the material to be treated. The SKR is used wherever continuous cleaning is required.
-An optional steam condenser can be integrated to extract steam vapors from the production area.
-De-oiling of the wash liquors and distillation of the rinsing liquids are optional equipment options.
-The waste heat generated from the distillative separation of substances is reused in an energy-efficient manner. It is used to heat the treatment baths of the spray chamber cleaning system.
-Filters and fans can also be integrated into the system as optional units
-An optional steam condenser can be integrated to extract steam vapors from the production area.
-De-oiling of the wash liquors and distillation of the rinsing liquids are optional equipment options.
-The waste heat generated from the distillative separation of substances is reused in an energy-efficient manner. It is used to heat the treatment baths of the spray chamber cleaning system.
-Filters and fans can also be integrated into the system as optional units
System type SKR-R (spray-circular chamber cleaning system - rotation)
Design of this plant:
The SKR-R type system is a combination of the SKR spray circular chamber cleaning system and the rotatable workpiece holder of an OMEGA rotary indexing cleaning system.
Procedure:
The workpieces are cycled (similar to the SKR system) through the individual stations located in the treatment tunnel.
In contrast to the SKR, however, the parts to be cleaned do not travel on a circular path but, similar to the OMEGA rotary cycle cleaning system, are fixed in rotating wash item holders and cycled in a circle.
The MTM cleaning system is particularly suitable for spray applications on parts with different geometries.
By fixing the workpieces once, it is also possible to clean through-holes and blind holes using a lance system. For the flood injection washing and rinsing process step, stationary hoods move over the workpiece that has been clocked into the treatment station, forming a chamber. The immersed workpieces are subjected to a highly turbulent flow. This ensures good rinsing of cavities and holes that are difficult to clean.
The parts cleaning system can be flexibly configured within the maximum weight, usable dimensions and materials of the items to be cleaned.
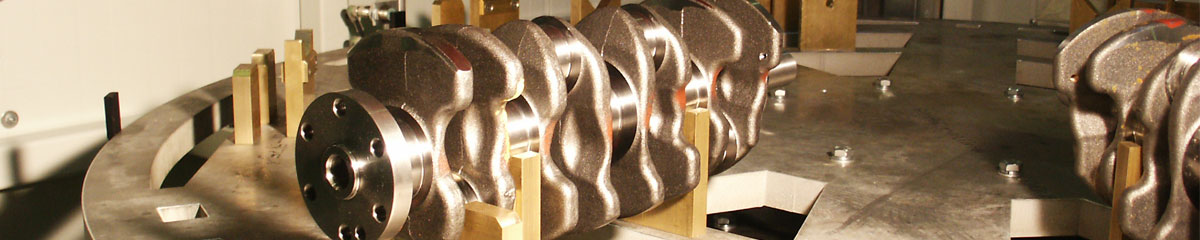
System type SKT (spray circular chamber cycle cleaning system)
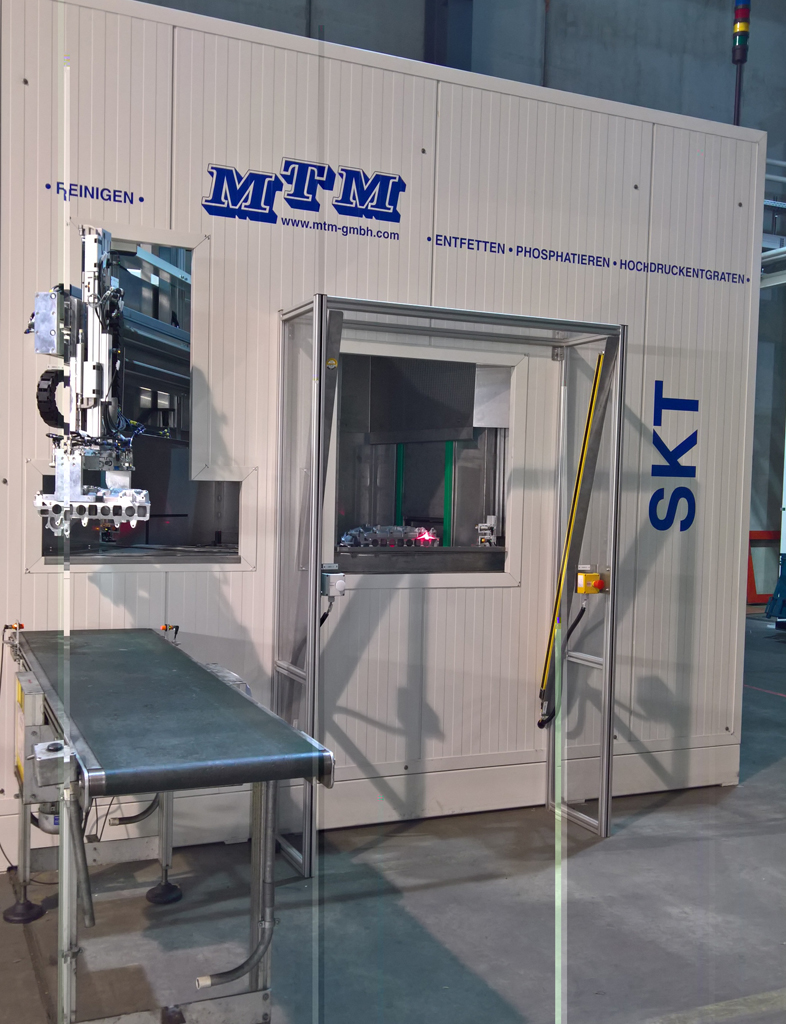
Requirements for the MTM cleaning system type SKT:
The SKT system is particularly suitable for spraying applications on workpieces with different geometries where high precision is required.
Außerdem ist die MTM
Similar to the SKR spray circular chamber cleaning system, the components or workpieces to be cleaned are guided along a circular path. However, they do not pass through the individual treatment zones, but are cycled from treatment station to treatment station in the closed tunnel. In the treatment tunnel, bulkheads are installed between the individual stations to prevent overspray into the adjacent areas.
Design of SKT:
The industrial parts cleaning system is designed for cleaning with a multi-stage spraying process as well as high-pressure deburring and subsequent drying.
The dripping liquid is fed back into the corresponding media tank. The treatment steps take place simultaneously and enable short cycle times of just a few seconds.
During spray washing, the items to be washed are exposed to the washing suds via the nozzle holders and soluble soiling is removed. The purpose of the subsequent spray rinsing is to remove the washing suds and the residual dirt bound in them from the parts. Targeted spraying of drilled holes or deburring of surfaces with high pressure is possible using optional deburring tools.
Due to the spray process used, only non-foaming aqueous or cold cleaning agents may be used as cleaning media.
The SKT system is particularly suitable for spraying applications on workpieces with different geometries where high precision is required.
Außerdem ist die MTM
Similar to the SKR spray circular chamber cleaning system, the components or workpieces to be cleaned are guided along a circular path. However, they do not pass through the individual treatment zones, but are cycled from treatment station to treatment station in the closed tunnel. In the treatment tunnel, bulkheads are installed between the individual stations to prevent overspray into the adjacent areas.
Design of SKT:
The industrial parts cleaning system is designed for cleaning with a multi-stage spraying process as well as high-pressure deburring and subsequent drying.
The dripping liquid is fed back into the corresponding media tank. The treatment steps take place simultaneously and enable short cycle times of just a few seconds.
During spray washing, the items to be washed are exposed to the washing suds via the nozzle holders and soluble soiling is removed. The purpose of the subsequent spray rinsing is to remove the washing suds and the residual dirt bound in them from the parts. Targeted spraying of drilled holes or deburring of surfaces with high pressure is possible using optional deburring tools.
Due to the spray process used, only non-foaming aqueous or cold cleaning agents may be used as cleaning media.
Design and process sequence:
The circular arrangement of the treatment stations makes it possible for the parts cleaning system to be loaded and unloaded at one position. The workpieces are placed on product carriers or as individual workpieces on permanently positioned holders. This precise positioning ensures accurate spray applications and high-pressure deburring of the various workpiece geometries. The spray circular chamber cycle cleaning system is flexible in terms of usable dimensions, maximum weight and materials of the parts to be cleaned. Components from the automotive industry in particular can be treated in the cleaning system. The space-saving cleaning system has a compact design and is suitable both as a decentralized stand-alone solution and for integration in production lines.
The circular arrangement of the treatment stations makes it possible for the parts cleaning system to be loaded and unloaded at one position. The workpieces are placed on product carriers or as individual workpieces on permanently positioned holders. This precise positioning ensures accurate spray applications and high-pressure deburring of the various workpiece geometries. The spray circular chamber cycle cleaning system is flexible in terms of usable dimensions, maximum weight and materials of the parts to be cleaned. Components from the automotive industry in particular can be treated in the cleaning system. The space-saving cleaning system has a compact design and is suitable both as a decentralized stand-alone solution and for integration in production lines.
Further options for the SKT system include the addition of ultrasound for particle removal and the integration of lance devices for the internal cleaning of through-holes or blind holes
The effectiveness of a vapor condenser can be used to prevent aerosols from escaping into the environment. In addition, the rinsing liquid can be treated by distillation.
Waste heat generated by the possible treatment options can be used again in an energy-efficient manner to heat the cleaning media.
The effectiveness of a vapor condenser can be used to prevent aerosols from escaping into the environment. In addition, the rinsing liquid can be treated by distillation.
Waste heat generated by the possible treatment options can be used again in an energy-efficient manner to heat the cleaning media.