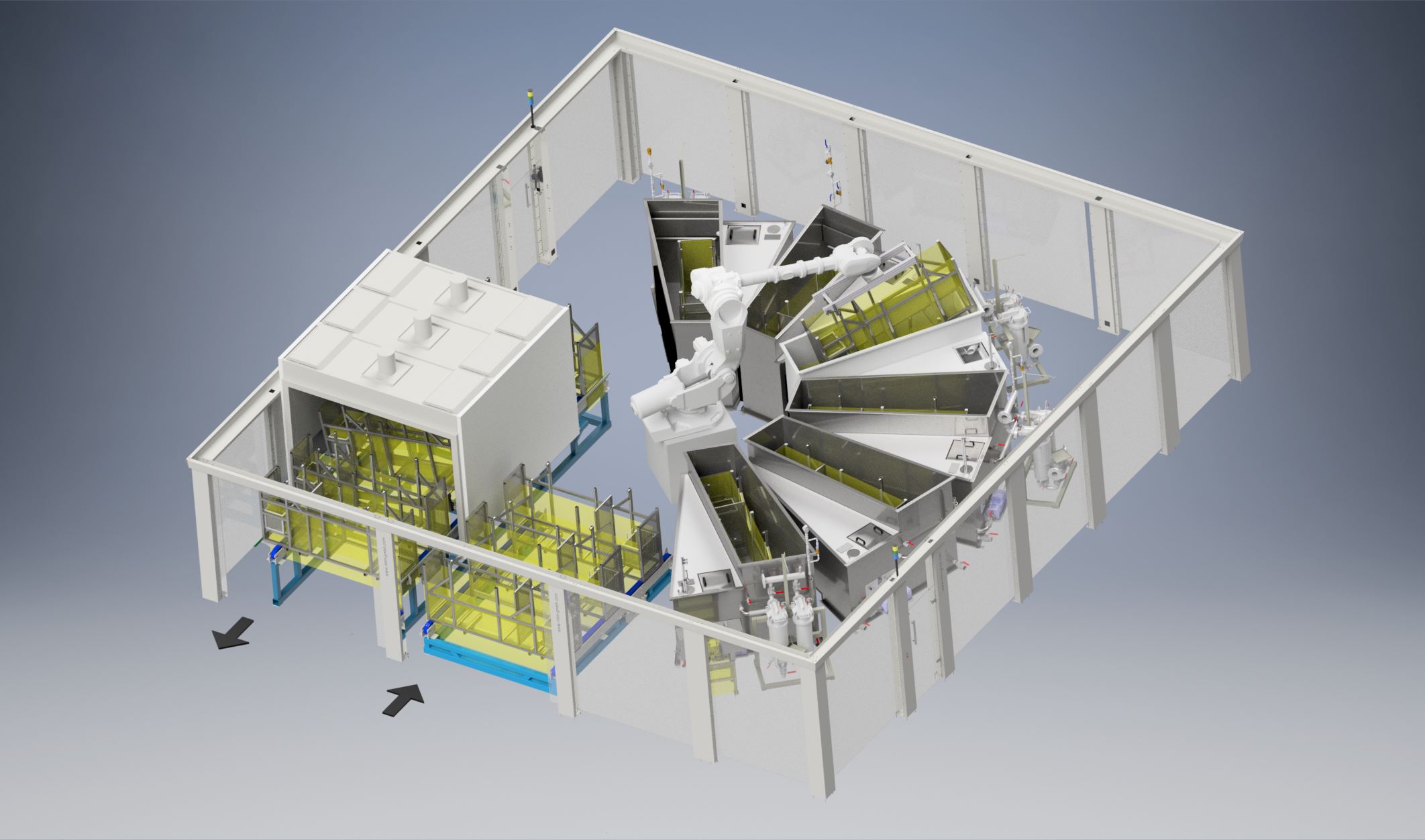
Systems for industrial fine and ultra-fine cleaning:
RTK (Robot immersion circular cleaning system)
Innovative cleaning solutions for the highest demands
MTM has developed the RTK (Robot Immersion Circular Cleaning System) - an industrial washing machine with patented technology that works on a galvanic and chemical basis. Our system combines the advantages of a proven industrial washing machine with the flexibility of a 6-axis robot. The treatment stations are arranged around the robot, which is responsible for handling the parts. This enables you to achieve energy savings of around 60% compared to standard market processes, for example when cleaning battery trays and battery boxes.
Technical highlights and advantages
MTM GmbH presents the ideal solution for your cleaning requirements. Whether you need a system for fine and ultra-fine cleaning or immersion cleaning processes, MTM has the right answer to your challenges. Our innovative cleaning systems are perfectly suited for a wide range of applications, from battery trays and optical glass to complex automotive parts such as engine blocks and turbochargers. With years of experience and customised solutions, MTM guarantees the best cleaning results for your specific needs, be it for the pre-treatment of bonding processes, the cleaning of implants or the processing of industrial parts of any kind. Our advanced technologies, such as flood injection cleaning and ultrasonic cleaning, ensure maximum efficiency and precision in every cleaning process.
Maximum flexibility:
The RTK system is ideal for ultrasonic cleaning, manganese coating, electroplating and chemical dipping processes, preservation processes, fine and ultra-fine cleaning, passivation (titanium coating), phosphating, titanium oxide coating, pre-treatment systems for bonding processes, aluminium bonding and more.Versatile use:
Ideal for applications such as aluminium bonding and use as a pre-treatment system for bonding processes.Environmentally friendly and energy savings of up to 60%:
Our systems conserve resources. Our technology ensures excellent results with energy savings of up to 60%.Automation:
An integrated 6-axis robot transports the workpieces between the treatment stations, ensures precise movements and minimises media carry-over through skilful handling.
Time optimisation:
The cycle time is optimised thanks to shorter robot paths and parallel processes such as loading and unloading, pre-cleaning and drying.Highest availability:
Thanks to the absence of mobile units, the system is extremely reliable and low-maintenance.Process sequence: precision and efficiency
- Loading and unloading station: Two separate storage areas for soiled and cleaned parts.
- Robot-assisted transport: 6-axis robot transports parts between the stations.
- Optimised cleaning: Movement of the parts during the process for maximum cleaning effect.
- Discharge: Cleaned parts are taken to the unloading station.
Areas of application: Versatile and cross-industry
The RTK system is ideal for cleaning and treating vehicle components, engine parts, metalworking and special applications.
Automobilindustrie:
Cleaning battery trays , axles , differential housings and engine blocks .
Elektroantriebstechnik:
Pre-treatment of aluminium rims , drive shafts , clutch housings and electric motors .
Maschinenbau:
Optimised cleaning of die-cast and milled parts, tools, cooling pipes and hydraulic fittings .
Get in touch with us
Find out more about our customised cleaning solutions.
Enquire now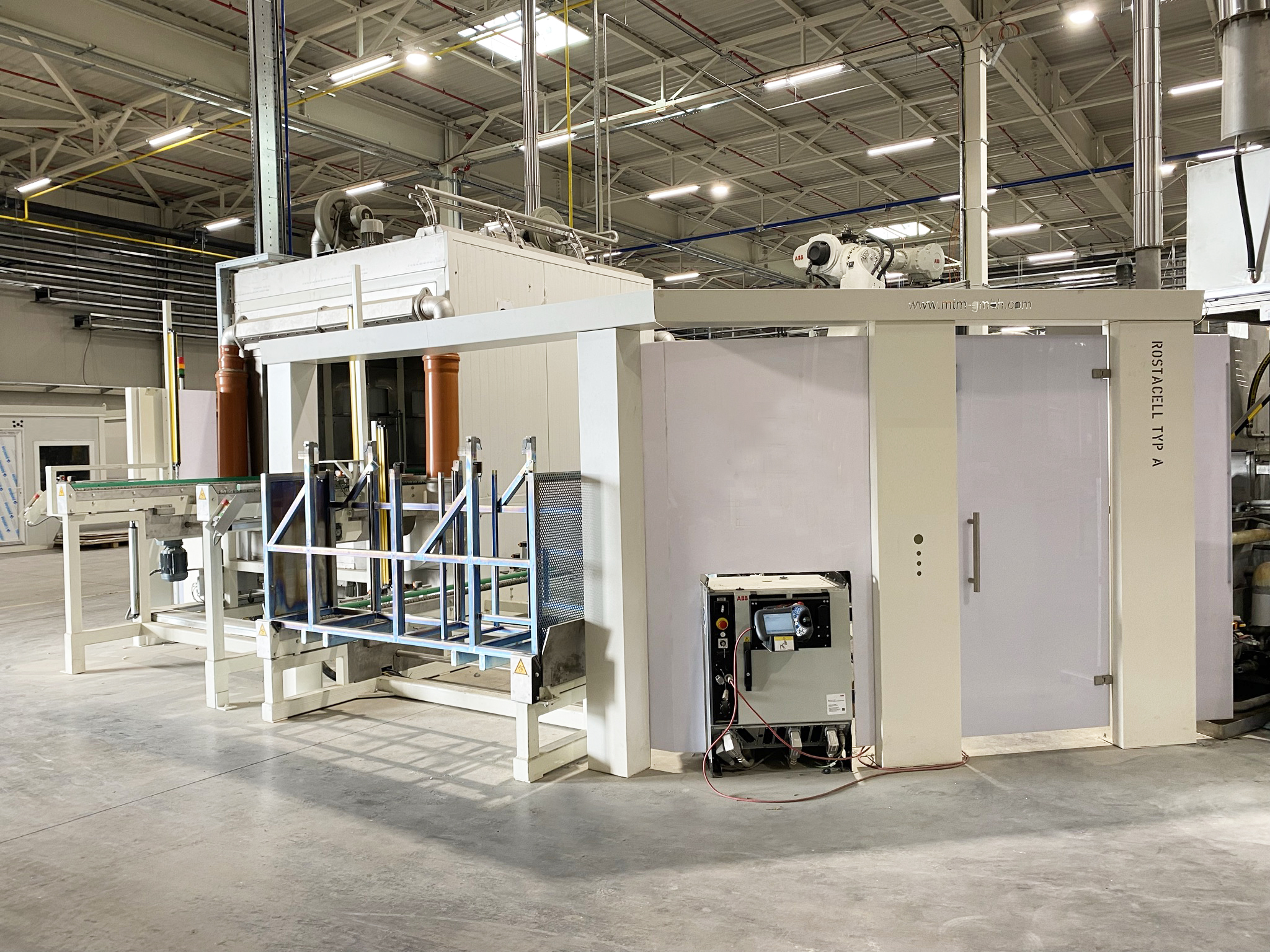
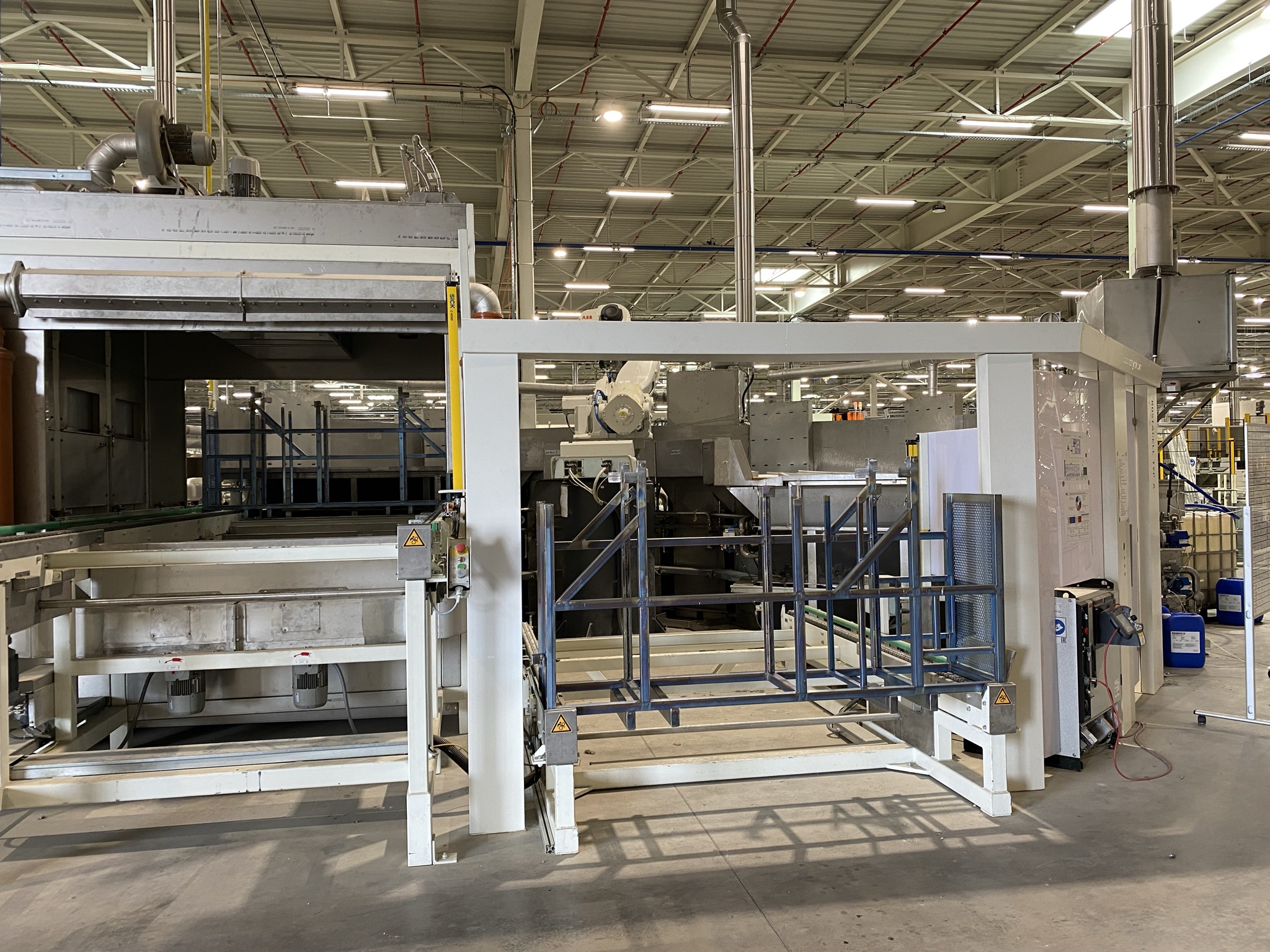
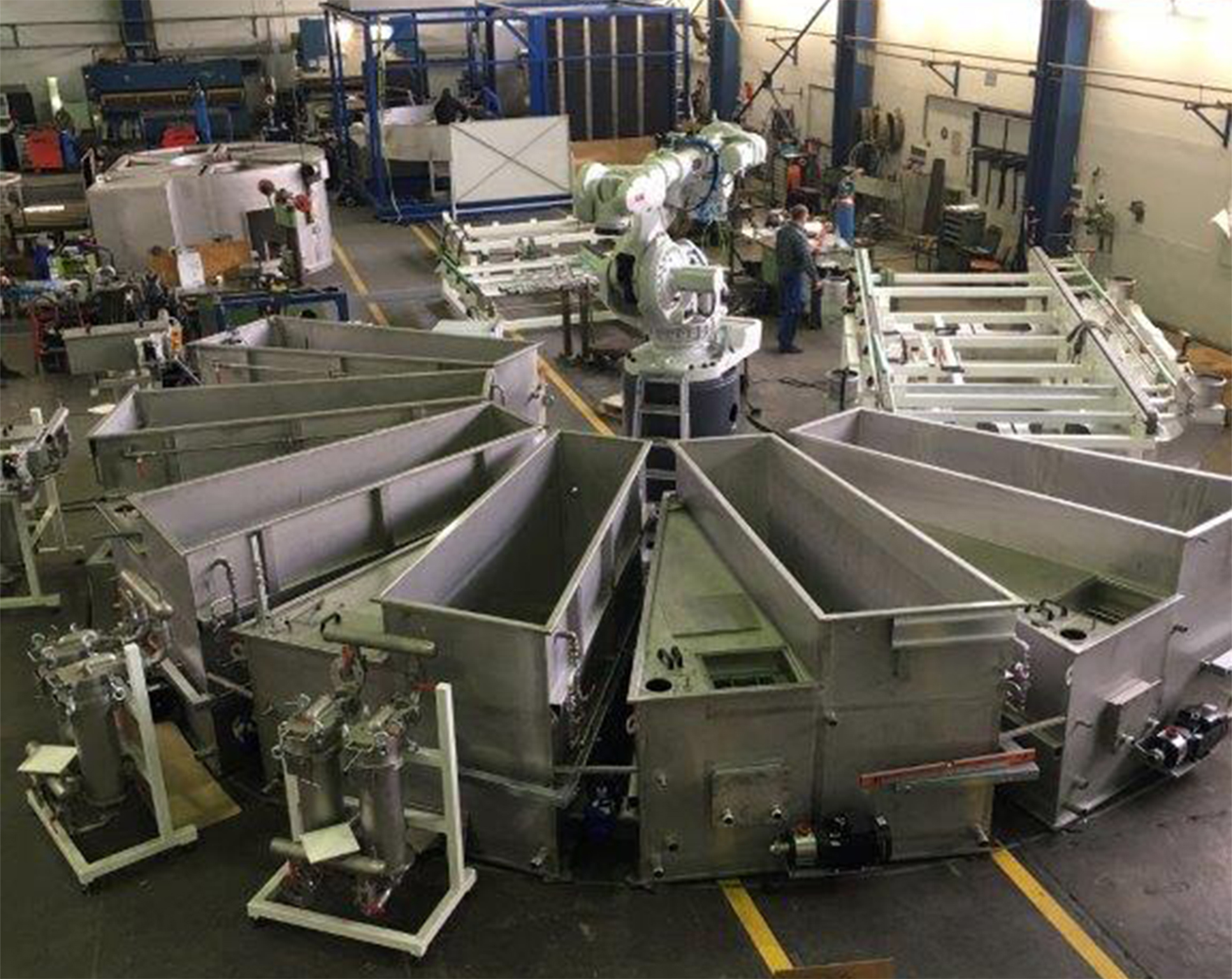
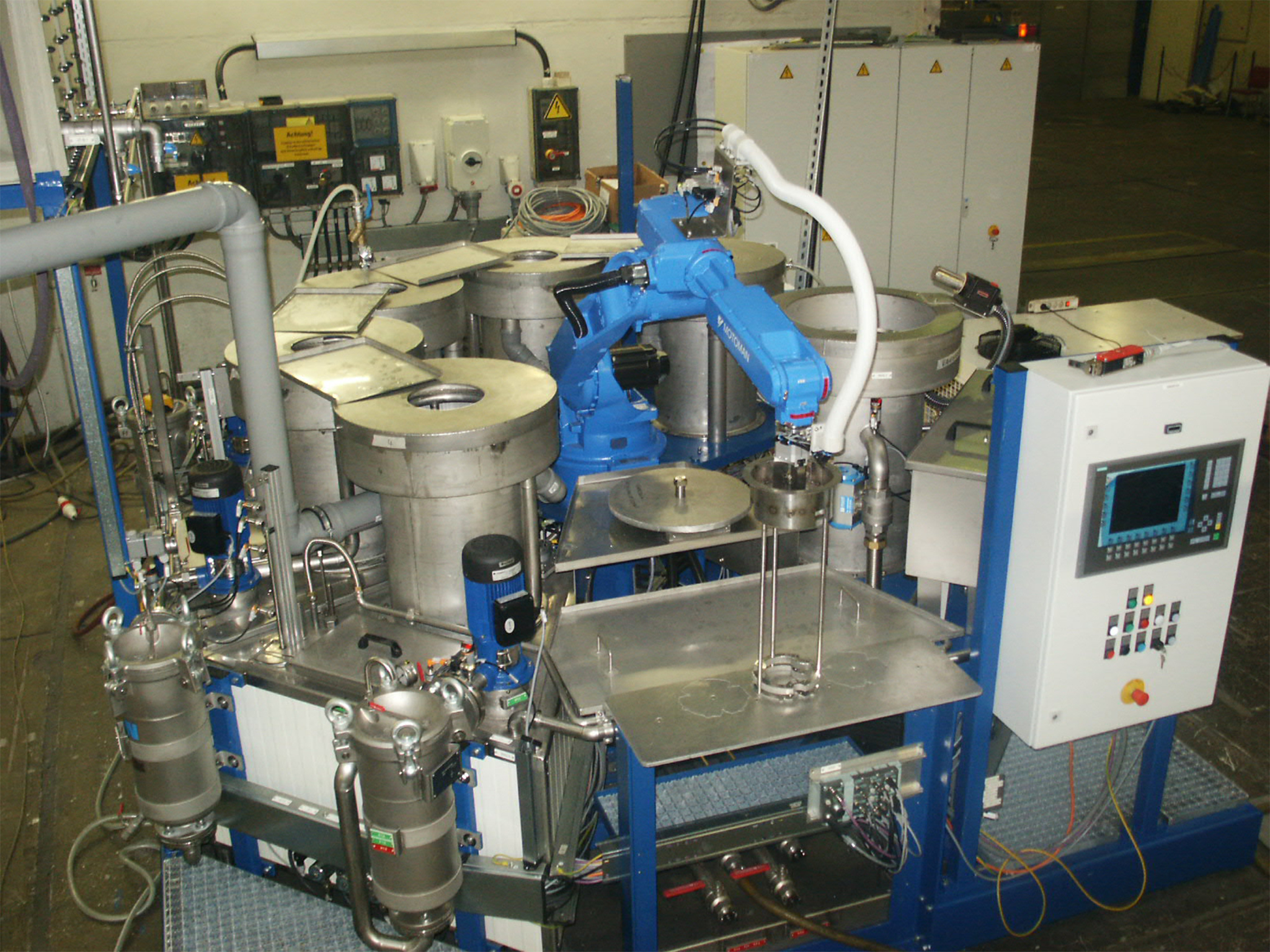
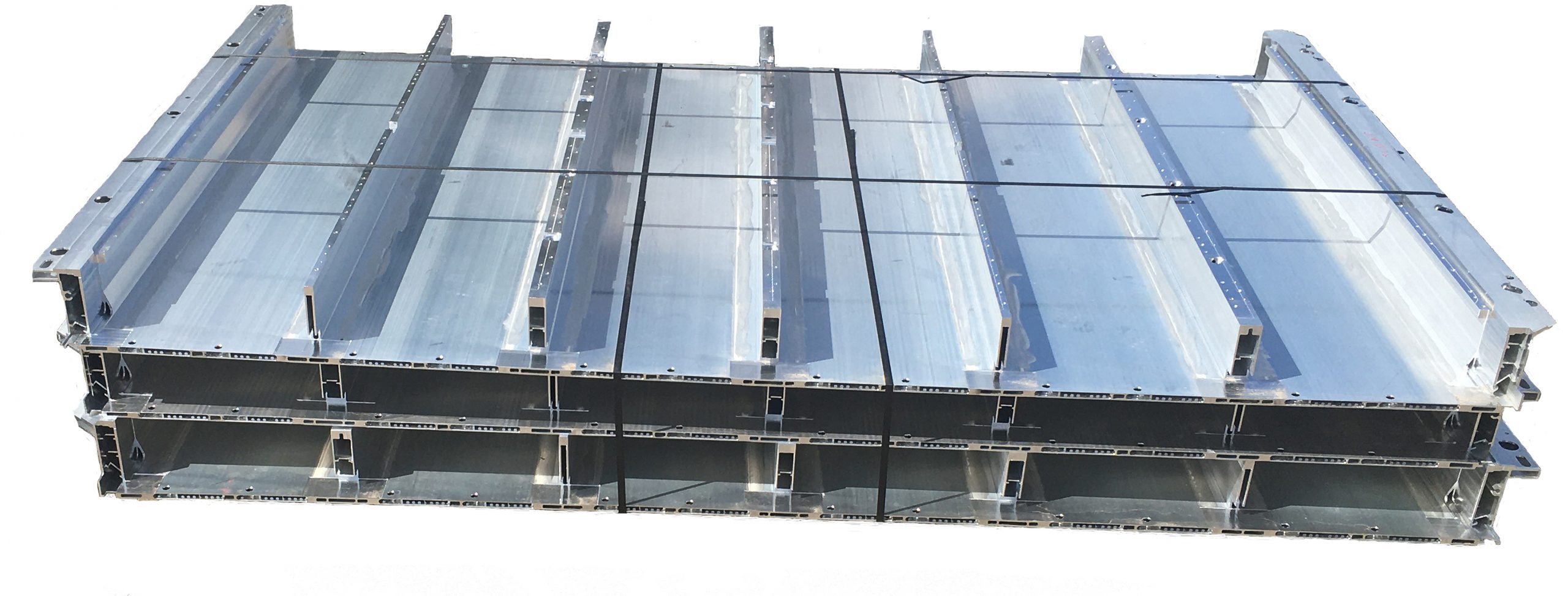